Technical Sharing | The Impact of Cutting Parameters on PCD Tools
SNSTC 2025-04-08
In modern manufacturing, polycrystalline diamond (PCD) tools are extensively employed in the machining of various difficult-to-cut materials—such as aerospace composites, automotive components, and 3C products—owing to their outstanding hardness, wear resistance, and thermal stability. To fully leverage the advantages of PCD tools and ensure high-quality machining performance, it is crucial to select cutting parameters rationally and precisely.
Cutting Speed
Cutting speed is one of the key factors affecting the performance of PCD tools. Appropriately increasing the cutting speed can improve machining efficiency, but excessively high speeds may cause a sharp rise in cutting temperature, reducing the strength and hardness of the tool material, accelerating tool wear, and even leading to tool tip breakage. Additionally, high-speed cutting can amplify machine vibrations, negatively impacting machining accuracy and surface quality. Therefore, selecting the optimal cutting speed requires a comprehensive consideration of factors such as workpiece material, tool material, and machine performance to achieve the best machining results and tool life.
Feed Rate
The magnitude of the feed rate directly influences machining efficiency and surface roughness. An increased feed rate enhances material removal rates but simultaneously enlarges the workpiece's residual surface area, resulting in higher surface roughness. Moreover, the greater cutting load induced can readily cause edge chipping. Conversely, an excessively reduced feed rate, while improving surface finish, elevates cutting temperatures and accelerates tool wear, thereby significantly shortening tool life. Consequently, determining an optimal feed rate necessitates balancing machining efficiency with quality requirements.
Cutting Depth
The depth of cut has a significant impact on the cutting force and heat generation when using PCD tools. While increasing the depth of cut can improve material removal rates, an excessive depth may lead to higher cutting forces and temperatures, accelerating tool wear and reducing tool life. In addition, an overly large depth of cut can easily cause tool edge chipping, which compromises machining stability. Therefore, when determining the appropriate depth of cut, factors such as the hardness of the workpiece material, the tool material and edge condition, and the machining method should be carefully considered to ensure both machining quality and tool life.
In summary, cutting parameters play a vital role in the performance of PCD tools. A rational selection of cutting speed, feed rate, and depth of cut can not only improve machining efficiency and quality but also extend tool life and reduce machining costs. In practical applications,it is important to continuously optimize cutting parameters based on specific machining conditions and workpiece materials to achieve the best results.
Contact us
SNSTC provides customized services for special tools, tool holders, fixtures, non-standard tool solutions tailored to diverse machining needs. In addition, we offer advanced five-axis laser machines for the production of PCD tools.We are dedicated to delivering the most suitable tooling solutions for every customer—fully meeting your machining requirements, reducing costs, and enhancing productivity.
We look forward to collaborating with you! If you have any questions or need more information, please feel free to contact us.
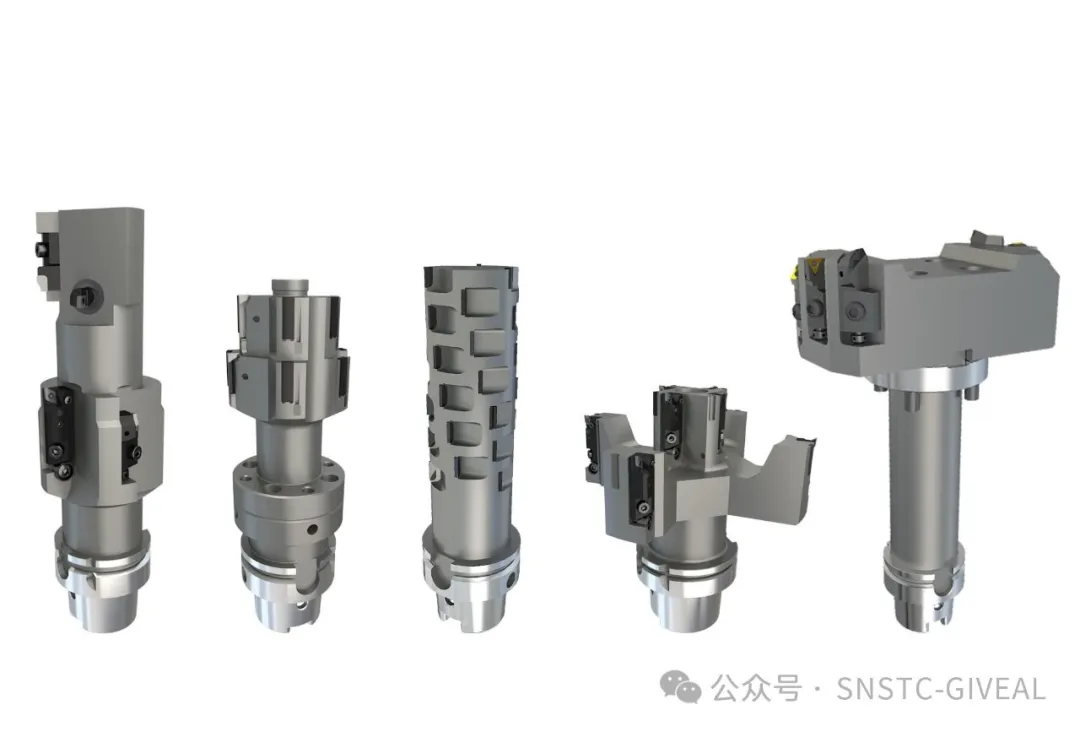